Fashion 3D Printer: 3D printing in fashion is changing the fashion landscape by introducing innovative and unique designs as well as eco-friendly practices. Several factors, such as the growth in the fashion industry and the demand for personalized designs, are expected to drive the 3D printing market to grow steadily between 2024 and 2029, from USD 17.5 billion to USD 37.4 billion.
Investing in such technology would be a great opportunity since it fosters creativity and reduces waste, which makes it a powerful force for future fashion.
Understanding 3D Printing Technology
Basic Principles of 3D Printing Technology
In fashion designing, 3D printing, also known as additive manufacturing, is revolutionizing the industry. It involves applying clear and creative design processes to computer-aided processes to create products from scratch.
In 3D printing, unique fit garments are designed and manufactured, which are often unavailable in stores. This process involves converting an image into a three-dimensional object, then cutting it into thin slices, and adding materials, like polymer or metal, repeatedly.
It minimizes wastage by using only the necessary amounts, and protects the environment by using biodegradable solvents. Thus, the designs are created and modified quickly, helping to meet the needs and demands of the customers immediately.
3D printing can fit one’s dimensions perfectly and is becoming a trend of the future as it embraces sustainability. Choosing the best 3d printer for small business helps ensure you get reliable quality while supporting eco-friendly practices.
Different Techniques Used in 3D Printing
Fused Deposition Modeling (FDM), Stereolithography (SLA), and Selective Laser Sintering (SLS) are three of the most common 3D printing techniques in the fashion industry.
Fused Deposition Modeling (FDM):
In FDM, plastic filaments are heated and extruded through nozzles to create parts. It is best for building quick prototypes. Designers can experiment with shapes and patterns without incurring high costs. It is useful for small fashion projects and self-made designers.
Stereolithography (SLA):
Using a laser, SLA solidifies liquid resin into shaped objects. This procedure is perfect for making jewelry and other fashionable items. SLA is able to support elaborate designs and allow high gloss finishes.
Selective Laser Sintering (SLS):
The SLS Aestheticism and Strength are combined to advance fashion design. It uses a laser to melt particulate materials to construct dense and complicated elements.
Designers can use 3D printing techniques to create eco-friendly new designs. They reduce waste and open up new horizons, helping those who want to make money from a 3D printer by offering unique, sustainable products.
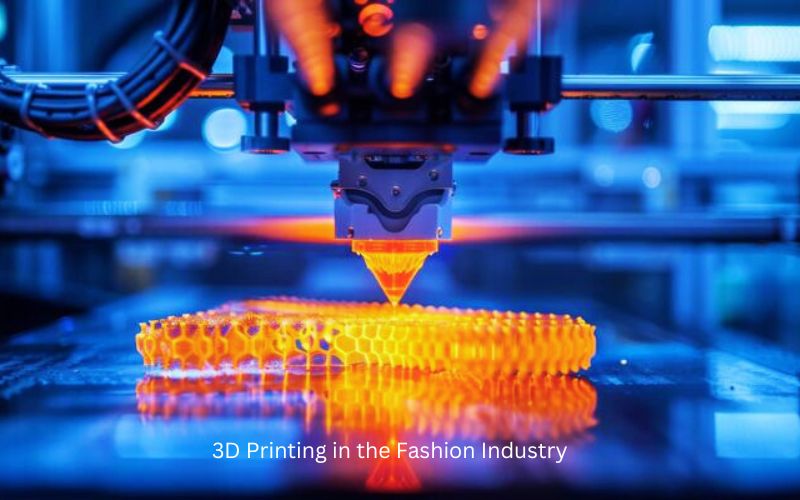
Benefits of 3D Printing in the Fashion Industry
Customization and Personalization
The 3D printing revolution is changing fashion by adding the element of customization and personalization, which most designers lack at the moment. Designers can manufacture tailored clothes using this technology, and each product is designed to suit its owner, based on the technology they use.
Using 3D printing, one can design a garment together. Designers can replicate intricate designs or surfaces that would otherwise be beyond the capabilities of non-computerized technologies using contemporary design software.
A single advantage of 3D printing is its ability to provide a perfect fit. Thanks to accurate fitting, 3D printing combines style with ease of wear. The fabrics are entirely unique and cannot be found in conventional clothing.
The 3D printing process still has challenges. Materials are limited, and clothing made in this process can be quite rigid compared to conventional alternatives. While many fail to offer research that evolves, materials that offer recyclable qualities are on their way.
3D printing will promote personalized fashion via customizable tech. This is a great trend, since we are on the verge of ethical one-off fashion.
Sustainability and Waste Reduction
As 3D printing becomes more popular, fashion is becoming more revolutionary. It also conserves resources by utilizing only what is needed; traditional methods will leave leftovers, but 3D printing won’t.
3D printing allows designers to create products just in time, which eliminates the need to have a large amount of unsold stock. Most designers nowadays use recycled materials when 3D printing, further reducing waste.
3D printed textile shows what is possible. Adidas uses 3D printing technology to manufacture shoes that reduce emissions, and designers like Iris van Herpen ensure minimal waste.
The fashion industry could be environmentally friendly for the first time since more brands are embracing 3D printing and improving sustainability.
Speed and Efficiency in Production
Fashion designers can convert concepts into actual designs more easily and faster with 3D prototyping, so they spend less time preparing models. Rapid prototyping enables designers to make rapid changes and iterations to designs.
Using 3D printing, consumers can stay current with new styling styles. The process allows for the development of new pieces and the improvement of existing ones.
Design teams can keep multiple samples in stock with a 3D prototype, since detailed actual models will represent the final design. This will improve coordination between the design and production departments, as well as reduce costs and make it more environmentally friendly.
Fashion is made faster and more effective through 3D prototyping. It allows designers to come up with new solutions in the most effective way without harming the environment.
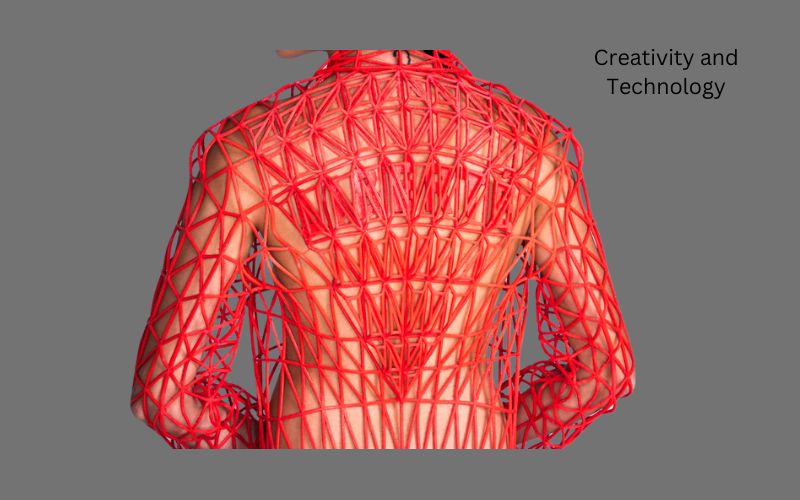
The Intersection of Creativity and Technology
Innovative Designs and Complex Structures
Using 3D printing to design is revolutionizing fashion. Iris van Herpen’s Crystallization Top is a top reminiscent of shells and illustrates nature’s magnificence. The top first hit the fashion market in 2010 as a convergence of science and art.
Julia Koerner’s Kelp outfit uses 3D printing techniques to create intricate patterns. She shows that the arts can be used in ways that go beyond their conventional applications. Designers can produce intricate and detailed designs much more easily with 3D printing, as these designs illustrate.
With 3D printing, the fashion industry is able to achieve things that were previously impossible. It enables quite a few of them to turn their imaginations into creations accurately. As a result of this new technology, designers will be able to achieve effortless innovation.
Collaboration between Designers and Technologists
As designers and technologists collaborate, the fashion world is revolutionized. Taking steps towards greening fashion is important as McCartney partners with Bolt Threads to develop new materials.
With this collaboration, designers are able to change colors or make clothing into a health monitoring device by inserting electronics on it. The result is products that are both functional and fashionable.
It is also revolutionizing the fashion industry. With AR, designers can visualize their ideas immediately and it reduces the number of dresses that need to be returned.
With AI in fashion, manufacturers make only what is needed, thus less waste, and fashion can be personalized and sustainable at the same time.
In the future, designers and technologists will form more partnerships, resulting in more advancements in fashion.
Challenges and Limitations of 3D Printing in Fashion
Material Limitations and Costs
A 3D printer for fashion is used to overcome spatial and financial limitations. In general, 3D printers use polymer materials like PLA and PETG. Although these materials are relatively inexpensive, they do not mimic traditional textile materials, so fashion designs are limited.
SLA printers use resins that are more expensive, between 50 and 400 dollars per liter. This makes complex shapes and large products more expensive.
In order for fashion 3D printing to become more popular and cost-effective, designers need to investigate better materials. Until then, designers will have to combine creativity with cost.
Technical Expertise and Accessibility
Fashion requires specialized knowledge. You need 3D modelling tools like CAD and Blender, which allow you to create and modify digital designs. Learning these tools allows you to bring your designs to life.
As well as technical knowledge, one must be able to use various types of 3D printers, including FDM printers and SLA printers, as well as troubleshoot some basic issues like warping.
Using evaluation skills, you can assure printed parts are within required quality standards. However, 3D printing is quite intricate, and one must remain current to remain relevant.
It will be possible for you to shape the fashion industry of the future and to expand the areas of imagination and invention by acquiring such skills.
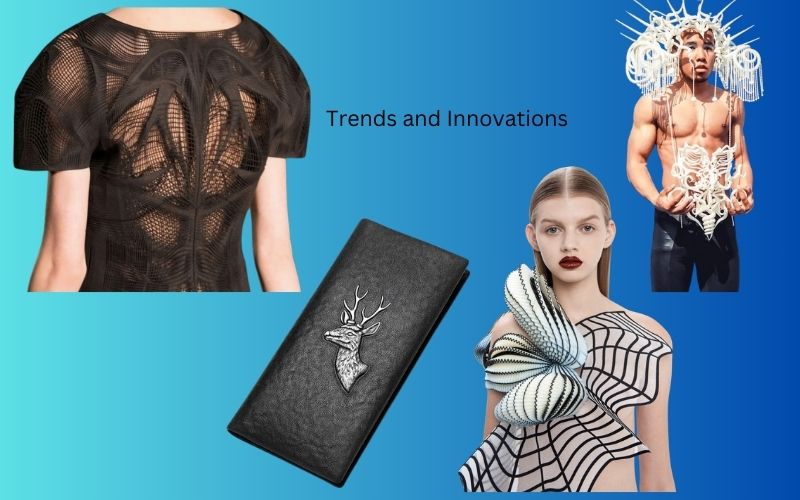
Future Trends and Innovations in 3D Fashion
Emerging Material Innovations
Using biodegradable & environmentally friendly materials, Bio-Flex & Sulapac are leading a revolution in 3D printing. Sulapac’s sustainable package uses wood fibers and biodegradable biopolymers. These materials are ideal for electronics and car parts.
This bioplastic is both flexible and tough, making it ideal for printing long-lasting items. It outperforms standard bioplastics like PLA. The use of biopolymers and natural fibers is capable of producing sustainable filaments that minimize waste while maintaining print quality.
Eco-friendly 3D printing encourages circular economy. The printed objects are compostable or recyclable, reducing dependence on fossil-based plastics. These materials will support 3D printing in reducing its carbon footprint as sustainable products become increasingly appealing.
Integration with Smart Technologies
Fashion has been revolutionized by smart fabrics. Electronic textiles have become a norm due to the integration of technology into clothes. These use the body to operate electronic devices without batteries. Fabrics are strengthened and thermally managed by graphene composites.
A wearable sensor allows for the monitoring of life signs. Using smart textiles, we can maintain our fitness. They also benefit the environment. In addition to being made from biodegradable materials, they consume less energy, thereby reducing waste.
Interactive fashion can now be designed to change color or pattern, and it is exciting to see the potential of this new revolution.
Unique Perspectives: Beyond the Common Narrative
Local Production and Decentralized Manufacturing
In fashion, 3D printing allows clothing to be manufactured or produced closer to their selling points, reducing logistics costs significantly. As a result, long distance shipping of items is reduced, reducing carbon emissions. Using a 3D printer, fashion trends can be made on demand, reducing waste and protecting the environment.
Intellectual Property and Design Ownership
It is very convenient to duplicate a design by using a digital file with the advent of 3D printing, which raises new ownership issues. A traditional IP law can easily protect 3D designs and these designs as long as they are protected by copyright.
In the future, digital watermarks and blockchains may prove useful in ensuring a design’s originality. Creating methods to protect designers’ rights is extremely important these days.
FAQ: Fashion 3D Printer
What are the benefits of 3D printing in fashion?
Custom designs are created quickly, and waste is reduced.
Is 3D printing cost-effective?
By reducing waste and inventory, it saves money in the long run.
How does it support sustainability?
Local production reduces emissions. Less material is used.
What design options are there?
Creating complex shapes is easy. Easy changes speed up the design process.
What challenges exist?
It is difficult to protect designs because of the high cost and skill requirements.
Can small businesses use it?
The price of small printers has fallen. They are now affordable.
How does it change supply chains?
On-demand production speeds up delivery and reduces overseas requirements.
Wrapping Up
Fashion 3D printing might aggressively develop creative and operational development in the industry by being more environmentally conscious. It reduces waste, reduces dependence on imports, and reduces transportation costs.
Furthermore, it facilitates new creativity, but in the current cyber environment, it is difficult to enforce ownership rights. In order to advance this technology, we would have to strike a balance between promoting creativity and protecting designs.
With these technologies advancements, the fashion industry will never be harnessed, but only enhanced, and take its next step towards efficient customisation.
Read more on this sites
Sovol SV01 Pro 3D Printer Review
Sovol SV06 Plus 3D Printer Review
Longer Orange 4K 3D Printer Review
Longer Orange 30 3D Printer Review