The ability to transform a 2D image into a 3D print opens up a world of creative possibilities, from personal keepsakes to professional prototypes. This process, often called “image-to-3D conversion,” involves translating visual data into a three-dimensional object that can be printed using 3D printing technology.
Whether you’re looking to preserve a cherished memory, create a custom gift, or develop a prototype for a business idea, converting pictures to 3D prints offers a tangible way to bring your ideas to life. With the right tools, you can easily convert picture to 3d print and bring your designs to life. For small businesses, investing in the best 3D printer for small business can significantly enhance the process, making it easier to produce high-quality, customized prints.
Applications in Personal Projects and Business Ventures
In personal projects, converting photos into 3D prints allows for creating unique items such as personalized gifts, custom jewelry, or commemorative plaques. This technology can be used for businesses to produce prototypes, create branded merchandise, or develop models for marketing and presentations. The versatility of 3D printing from images makes it a valuable tool across various industries, including art, fashion, education, and marketing.
Benefits: From Personalized Gifts to Prototyping
The primary benefits of converting pictures to 3D prints include personalization, customization, and rapid prototyping. Personalized items carry sentimental value, making them ideal for gifts or commemorations. Customization allows creating one-of-a-kind designs tailored to specific needs or preferences. Rapid prototyping lets businesses quickly iterate on product designs, reducing development time and costs. Whether for personal or professional use, the ability to Instantly Create a 3D Model from a simple image empowers creators to turn photos into tangible, functional objects with ease.
Step 1 – Preparing Your Image for 3D Conversion
Selecting the Ideal Image
- High-Resolution and Clear Contrast: Choose images with high resolution and clear contrast to ensure that details are captured accurately during the conversion process.
- Simple Backgrounds Enhance Accuracy: Opt for images with simple, uncluttered backgrounds to prevent distractions and ensure that the focus remains on the subject.
- Avoiding Complex Patterns and Gradients: Images with complex patterns or gradients can be challenging to convert into 3D models. Simpler images yield better results.
Editing the Image for Optimal Results
- Converting to Black and White for Clarity: Converting the image to black and white can help in defining edges and contrasts, making it easier to create a 3D model.
- Using Tools Like GIMP or Photoshop for Adjustments: Utilize image editing software such as GIMP or Photoshop to adjust brightness, contrast, and sharpness, enhancing the quality of the image. These adjustments are essential when you convert picture to 3d print, as they help highlight important details and improve the final 3D model’s accuracy.
- Creating Vector Outlines with Inkscape or Illustrator: For more detailed work, convert the image into vector outlines using tools like Inkscape or Illustrator, which can then be used in 3D modeling software.
Step 2 – Choosing the Right Method for Conversion
Manual 3D Modeling with Blender or Tinkercad
- Importing and Extruding Vector Files: Import the vector outlines into 3D modeling software like Blender or Tinkercad and use extrusion techniques to add depth to the design.
- Applying Displacement Mapping for Depth: Use displacement mapping to add realistic depth and texture to the model, enhancing its visual appeal.
- Sculpting and Refining the Model: Refine the model by sculpting details and smoothing surfaces to achieve the desired look.
Automated Conversion Using AI Tools
- Utilizing Platforms Like Alpha3D for Quick Conversion: AI-powered platforms like Alpha3D can automatically convert 2D images into 3D models, streamlining the process.
- Adjusting Parameters: Resolution, Scale, and Mesh Density: Customize the output by adjusting parameters such as resolution, scale, and mesh density to suit your specific needs.
- Previewing and Downloading the STL File: Preview the generated 3D model to ensure it meets your expectations before downloading the STL file for printing.
Lithophane Technique for Photo Reliefs
- Creating 3D Photo Prints with Backlighting: Lithophanes are 3D prints that reveal detailed images when backlit, creating a unique visual effect.
- Using Online Tools Like 3DP Rocks for Conversion: Online tools like 3DP Rocks allow you to upload a photo and convert it into a lithophane-ready 3D model.
- Adjusting Settings for Desired Thickness and Detail: Customize the lithophane by adjusting settings such as thickness and detail level to achieve the desired effect.
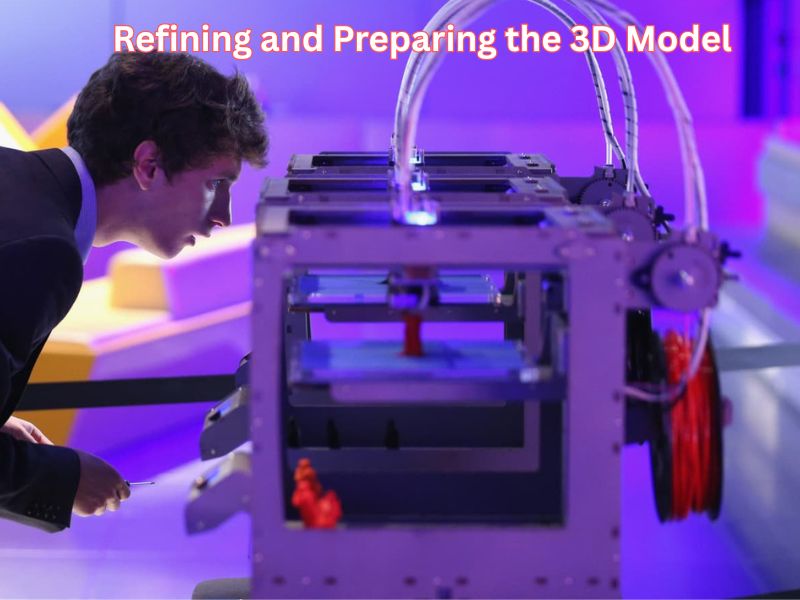
Step 3 – Refining and Preparing the 3D Model
Mesh Repair and Optimization
- Using MeshLab or Blender for Error Checking: Utilize tools like MeshLab or Blender to check for and repair any errors in the mesh, ensuring the model is printable.
- Ensuring Watertight Geometry for Printing: Ensure that the model’s geometry is watertight, meaning there are no holes or gaps, to prevent printing issues.
- Adjusting Wall Thickness and Adding Supports: Modify wall thickness and add support structures as needed to ensure the model prints correctly.
Texture Mapping and UV Unwrapping
- Applying 2D Images onto 3D Models: Use texture mapping to apply 2D images onto the 3D model, adding realism and detail.
- Flattening the Model for Accurate Mapping: Flatten the 3D model using UV unwrapping techniques to accurately map textures onto the surface.
- Enhancing Realism with Proper Texturing: Enhance the model’s realism by carefully applying textures and adjusting settings to achieve the desired appearance.
Step 4 – Exporting and Printing the 3D Model
Exporting in Compatible Formats
- Choosing Between STL, OBJ, or FBX: Select the appropriate file format for your 3D printer and software. STL is commonly used for 3D printing, while OBJ and FBX are suitable for more complex models. If you’re planning to convert picture to 3d print, make sure the format you choose is compatible with both your modeling tool and your printer.
- Adjusting Export Settings for Printer Compatibility: Ensure that export settings match your printer’s specifications, such as scale and orientation.
- Saving the File for Printing: Save the exported file to a location accessible to your 3D printer, ready for the printing process.
Printing the Model
- Selecting the Right Material: PLA, ABS, or Resin: Choose the appropriate material based on the model’s requirements and the capabilities of your 3D printer.
- Choosing the Appropriate Printer Settings: Set printer parameters such as layer height, print speed, and temperature to optimize print quality.
- Monitoring the Print Process for Quality Assurance: Monitor the printing process to ensure that the model is printing correctly and to address any issues that may arise.
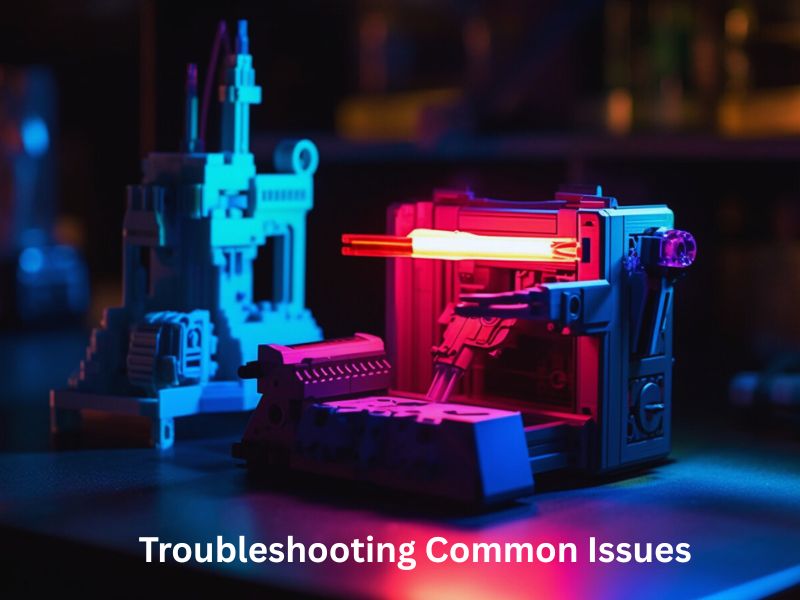
Step 5 – Troubleshooting Common Issues
Addressing Mesh Errors
- Identifying and Fixing Holes or Gaps: Use mesh repair tools to identify and fix any holes or gaps in the model’s geometry, ensuring it is watertight.
- Using Repair Tools for Quick Fixes: Utilize automated repair tools to quickly fix common mesh errors, saving time and effort.
Optimizing Print Quality
- Adjusting Print Speed and Temperature: Modify print speed and temperature settings to achieve optimal print quality and reduce issues such as warping or stringing.
- Ensuring Proper Layer Adhesion: Ensure that each layer adheres properly to the previous one by adjusting settings such as bed temperature and first layer height.
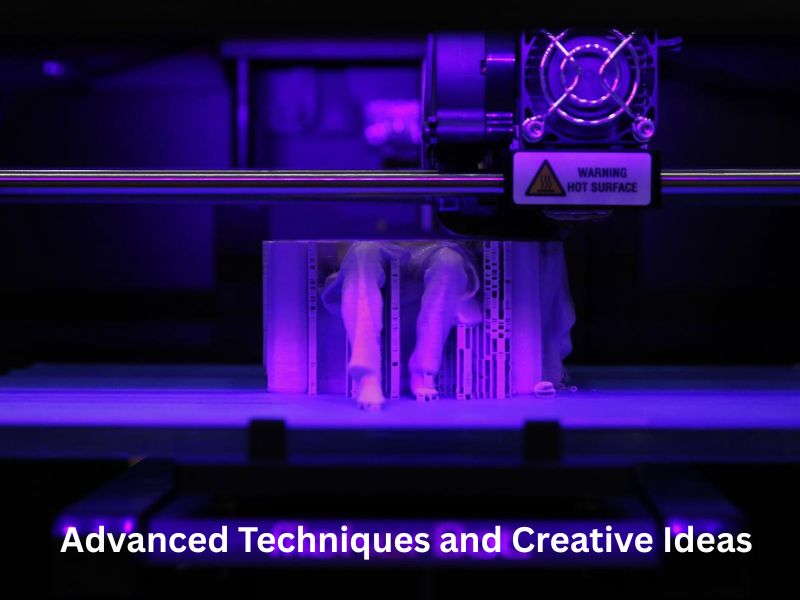
Bonus Tips – Advanced Techniques and Creative Ideas
Creating 3D Models from Multiple Images
- Using Photogrammetry Software for Detailed Models: Capture multiple images of the subject from different angles and use photogrammetry software to convert picture to 3d print and create a detailed 3D model.
- Capturing Multiple Angles for Comprehensive Data: Ensure that images cover all angles of the subject to provide comprehensive data for accurate modeling.
Exploring 3D Scanning for Physical Objects
- Using Smartphone Apps or Dedicated Scanners: Utilize smartphone apps or dedicated 3D scanners to capture the geometry of physical objects for conversion into 3D models. These digital tools make it easier to convert picture to 3d print by generating accurate depth data that can be turned into printable designs.
- Converting Scanned Data into Printable Models: Process the scanned data using 3D modeling software to create printable models ready for 3D printing.
Incorporating Animation into 3D Prints
- Designing Models with Moving Parts: Incorporate moving parts into your 3D models, such as hinges or gears, to create interactive prints.
- Using 3D Printing Techniques for Functional Models: Utilize 3D printing techniques such as overhangs and supports to create functional models with moving parts.
FAQs: convert picture to 3d print
1. Can I convert a single photo into a 3D print?
Yes, it’s possible to convert picture to 3d print, though the results may be limited in detail. Tools like Smoothie-3D and Image to Lithophane can assist in this process. However, for more detailed and accurate models, multiple images or advanced techniques are recommended.
2. What is a lithophane, and how do I create one?
A lithophane is a 3D print that reveals a detailed image when backlit. To create one, use tools like Image to Lithophane or Cura. These tools convert your image into a 3D model with varying thicknesses, representing different shades of gray.
3. How do I prepare my image for 3D conversion?
- High Resolution: Ensure your image has a high resolution to capture fine details.
- Simple Background: Opt for images with simple backgrounds to enhance accuracy.
- Contrast: Images with clear contrast between the subject and background yield better results.
4. What software can I use to convert images to 3D models?
- Smoothie-3D: An online tool that allows you to create 3D models from a single image.
- Image to Lithophane: A tool for creating lithophanes from images.
- Blender: A free, open-source 3D modeling software suitable for detailed conversions.
- Fusion 360: A professional CAD software that offers advanced modeling features.
5. How do I ensure my 3D model is printable?
- Check Mesh Integrity: Use tools like MeshLab or Blender to check for holes or non-manifold edges.
- Optimize Geometry: Simplify complex geometries to reduce printing errors.
- Adjust Wall Thickness: Ensure walls are thick enough to be printed without collapsing.
6. What file formats are compatible with 3D printers?
Common file formats include STL, OBJ, and FBX. STL is widely used for 3D printing due to its simplicity and compatibility.
7. What materials are best for 3D printing photos?
- PLA: Easy to print and suitable for most models.
- Resin: Offers high detail and smooth finishes, ideal for small or intricate models.
- ABS: Durable and heat-resistant, suitable for functional parts.
8. How do I print my 3D model?
- Slice the Model: Use slicing software like Cura or PrusaSlicer to prepare your model for printing.
- Set Printer Parameters: Adjust settings such as layer height, print speed, and temperature based on your material and printer.
- Monitor the Print: Keep an eye on the printing process to address any issues promptly.
9. Can I create a 3D model from multiple images?
Yes, using photogrammetry techniques, you can create detailed 3D models from multiple images taken from different angles. Software like Autodesk ReCap or Meshroom can assist in this process, especially if you’re looking to convert picture to 3d print with higher accuracy and depth.
10. Are there AI tools for converting images to 3D models?
Yes, AI-powered tools like TripoSR can convert 2D images into 3D models. These tools use machine learning algorithms to infer depth and structure from a single image.
Wrapping Up
Convert picture to 3d print offers a creative way to bring images to life, whether for personal keepsakes or professional prototypes. By selecting high-resolution images, editing them for clarity, and choosing the appropriate conversion method—be it manual modeling, AI tools, or lithophane techniques—you can transform 2D visuals into tangible 3D objects. Refining the 3D model ensures quality, while exporting and printing it brings your creation into the physical world. With advancements in technology and accessible tools, this process has become more approachable, enabling individuals and businesses to explore new dimensions in design and personalization.